Le brasage est le processus le plus important dans le processus de substrat de nitrure de silicium AMB, et la préparation du métal d'apport de brasage actif et du brasage du métal actif sont actuellement les points clés et difficiles.
Ti, Zr, Hf, V, Nb, etc. sont des éléments métalliques actifs courants qui peuvent infiltrer les substrats en nitrure de silicium et sont largement utilisés pour l'étanchéité active entre la céramique et les métaux. Parmi eux, l’alliage Ag-Cu-Ti avec Ti comme élément actif est le métal d’apport actif le plus étudié et le plus utilisé. Il peut mouiller la plupart des surfaces en céramique à une température de 800 ~ 950 °C, et la tête de brasage a une résistance élevée et des performances stables, de sorte que l'étanchéité entre la céramique et les métaux, la céramique et la céramique puisse être mieux réalisée.
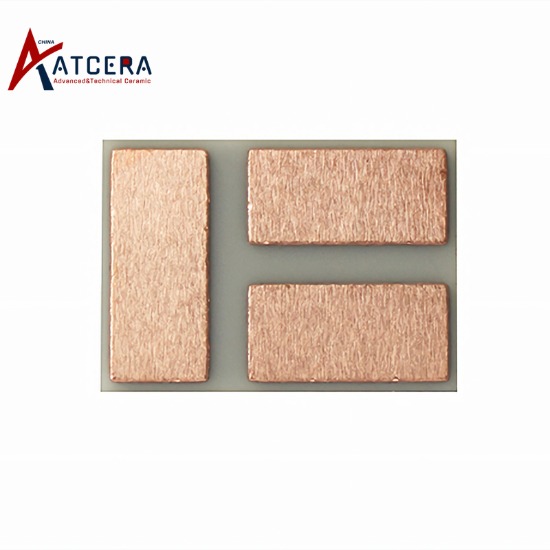
L'utilisation du métal d'apport actif Ag-Cu-Ti comprend les quatre formes suivantes, qui varient en fonction de la forme de l'élément Ti et de la combinaison du métal d'apport :
a. Pâte de poudre de Ti pré-enduite (ou TiH, poudre), puis ajoutez de la soudure préformée (généralement de la soudure en alliage Ag72Cu28) ;
b. Une couche de film de Ti est déposée au préalable sur la surface céramique avec PVD (dépôt physique en phase vapeur) ou CVD (dépôt chimique en phase vapeur), puis un métal d'apport Ag-Cu est ajouté.
c. Utilisez de la soudure Ag-Cu-Ti ;
d. Utilisez de la pâte à souder Ag-Cu-Ti.
Lors de l'utilisation d'un métal d'apport actif argent-cuivre-titane pour préparer un substrat en nitrure de silicium AMB, les principales causes de vides interfaciaux sont les suivantes :
1. Qualité de surface des matières premières : les rayures, les piqûres, l'oxydation, la pollution organique sur la surface de la céramique et du cuivre sans oxygène avant le soudage auront un impact négatif sur le mouillage et l'étalement de la soudure, entraînant un risque potentiel de vides à l'interface brasée. .
2. Qualité d'impression de soudure : lors du processus d'impression de pâte à souder sur de grandes surfaces, il est facile d'avoir le problème de fuite de pâte à souder et d'impression inégale, et une fois la soudure fondue, cela entraînera directement la formation de trous.
3. Désactivation des éléments actifs : l'élément actif Ti dans la pâte à souder AgCuTi est très sensible à l'oxygène, et le degré de vide doit souvent être supérieur à 10-3 Pa dans le processus de brasage à haute température. Si le degré de vide ne peut pas répondre aux exigences de soudage, le Ti est oxydé et désactivé, et la soudure ne peut pas mouiller la surface en céramique, ce qui provoquera une grande zone de soudage, des fuites de soudage et d'autres phénomènes.
4. Gaz volatil de la pâte à souder : lors du processus de brasage, le gaz volatilisé dans la pâte à souder sera enveloppé par le flux pour former des bulles. De plus, la réaction des acides organiques et des oxydes métalliques dans le flux produira également des bulles. avec la réaction des bulles progressivement plus grandes, les bulles déchargées laisseront des pores denses sur la surface de la pâte à souder, et les bulles non déchargées resteront également à l'interface de brasage avec le processus de fusion et de solidification de la soudure. Former un vide.
5. Paramètres du processus de brasage : le métal d'apport de brasage actif Ag-Cu-Ti est souvent supérieur à 800 â pour mouiller la surface du Si3N4, si la température de brasage est trop basse ou le temps de maintien est trop court, la réaction entre le Ti et la surface en céramique n'est pas suffisant, ce qui fait que le métal d'apport de brasage ne peut pas mouiller complètement la surface en céramique.
En résumé, le brasage est crucial pour les substrats en nitrure de silicium AMB, avec l'alliage Ag-Cu-Ti comme principal métal d'apport actif en raison de sa capacité à mouiller la céramique à 800 ~ 950 °C et à former des joints solides. Cependant, les vides interfaciaux constituent un problème important causé par des facteurs tels que la qualité des matières premières, l'impression des soudures, la désactivation des éléments actifs, les gaz volatils et les paramètres de brasage inappropriés. Pour obtenir des joints de haute qualité, il est essentiel de relever ces défis grâce à une préparation raffinée, des techniques améliorées, des conditions optimisées et un contrôle amélioré des processus.