Aujourd'hui, avec le développement rapide de l'industrie électronique, les céramiques de nitrure d'aluminium sont devenues le premier choix pour les substrats de refroidissement de circuits intégrés et les matériaux d'emballage à grande échelle en raison de leur excellente conductivité thermique, de leurs excellentes propriétés mécaniques, de leur résistance à la corrosion et de leurs bonnes propriétés électriques. En particulier dans la recherche de miniaturisation et de puces de circuits intégrés hautes performances, la surface légère et ultra-lisse des substrats en nitrure d'aluminium devient la clé pour améliorer les performances globales. Cependant, la dureté élevée, la fragilité élevée et la faible ténacité de la céramique de nitrure d'aluminium ont posé de grands défis à son usinage d'ultra-précision. Comment obtenir une rugosité de surface aussi faible que le niveau nanométrique sans endommager le matériau lui-même est devenu un problème technique à résoudre de toute urgence dans la recherche scientifique et dans l'industrie. Cet article se concentre sur le processus de polissage magnétorhéologique des céramiques de nitrure d'aluminium et explique comment relever efficacement ces défis et obtenir des surfaces usinées plates de haute qualité.
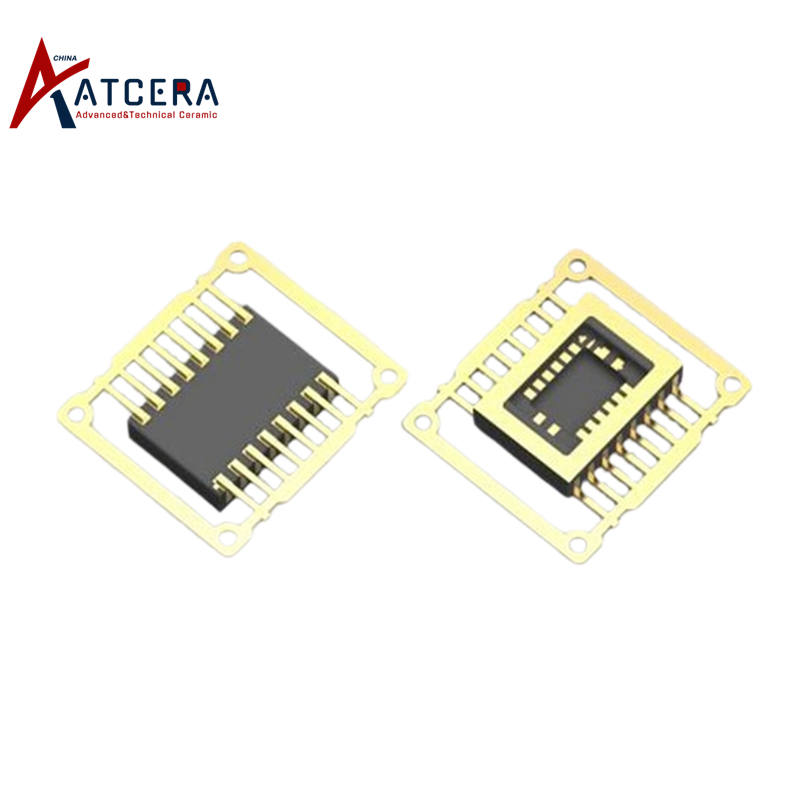
La technologie de polissage magnétorhéologique, en tant que méthode d'usinage innovante d'ultra-précision, combine intelligemment les principes de contrôle du champ magnétique et de mécanique des fluides pour obtenir un polissage sans contact ou à faible contrainte de contact des surfaces des matériaux. En ajustant l'intensité et la distribution du champ magnétique, la disposition et le mouvement des particules magnétiques dans le fluide magnétorhéologique sont contrôlés pour former un film de polissage dynamique et contrôlable sur la surface de la pièce. Ce film de polissage peut éliminer de minuscules bosses sur la surface du matériau avec une précision et une efficacité extrêmement élevées sous une très faible pression de contact, atteignant une rugosité de surface de l'ordre du nanomètre.
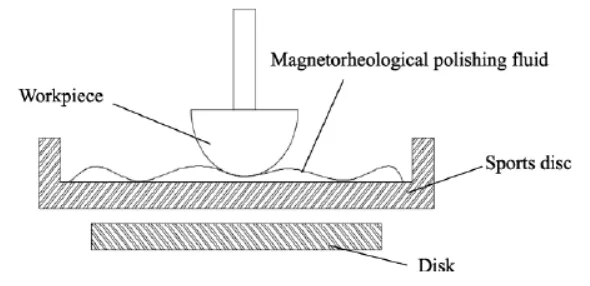
Pour les céramiques au nitrure d’aluminium, la technologie de polissage magnétorhéologique a montré des avantages significatifs. Tout d'abord, puisqu'il n'y a presque pas de contact direct dans le processus de polissage, les contraintes mécaniques et thermiques pouvant être causées par les méthodes de polissage traditionnelles sont évitées et les défauts de surface et les dommages souterrains générés pendant le traitement sont considérablement réduits. Deuxièmement, le polissage magnétorhéologique présente un degré élevé de contrôlabilité. En ajustant avec précision les paramètres du processus, tels que l'intensité du champ magnétique, le débit du fluide de polissage et la vitesse de l'échantillon, il peut réaliser un usinage précis de substrats en céramique de nitrure d'aluminium de différentes formes et tailles pour répondre à divers besoins de traitement.
De plus, la technologie de polissage magnétorhéologique présente également un taux d’enlèvement de matière et une efficacité de traitement élevés. Les résultats montrent que dans des conditions de traitement appropriées, le processus de polissage magnétorhéologique des céramiques de nitrure d'aluminium peut atteindre une précision de surface d'une valeur RMS inférieure à 2 nm, tout en maintenant une vitesse de traitement élevée, ce qui est d'une grande importance pour améliorer l'efficacité de la production et réduire les coûts de production.
En résumé, le processus de polissage magnétorhéologique des céramiques de nitrure d'aluminium, avec son mécanisme unique de polissage sans contact ou à faible contrainte de contact, surmonte efficacement les problèmes de traitement causés par la dureté élevée, la fragilité élevée et la faible ténacité des céramiques de nitrure d'aluminium, et offre un nouveau solution pour obtenir des surfaces usinées planes de haute qualité. Avec la maturité et l'optimisation continues de la technologie, la technologie de polissage magnétorhéologique devrait montrer son grand potentiel dans davantage de domaines tels que l'emballage électronique, les composants optiques, les machines de précision, et promouvoir le développement d'industries connexes dans le sens d'une plus grande précision et d'une plus grande efficacité. À l'avenir, nous sommes impatients d'élargir encore le champ d'application de la technologie de polissage magnétorhéologique grâce à une recherche et une innovation continues, et de contribuer davantage au progrès scientifique et technologique et au développement social.